Additively manufactured carbon reinforced concrete structures supported with free-standing textile formwork – freeDome
Additive manufacturing, also for carbon-reinforced concrete, is receiving more and more attention in the construction industry. The advantage of additive manufacturing is the elimination of formwork and the high freedom of movement of the robots, which enable the production of complex geometries. Curves or curved walls can thus be produced without complex formwork construction, although overhanging or horizontally unsupported components such as window lintels, beams, ceilings or shells cannot currently be produced additively. Due to its low dead weight and high load-bearing capacity, carbon-reinforced concrete is in principle excellently suited for the production of ceilings and shells. However, the production of complex shapes is limited by the expense of formwork construction and the manpower required during the lamination process.
The idea presented here is to combine the strengths of both construction methods while excluding the weaknesses. The aim is to erect shell structures with a minimum of material, whereby the method is extremely innovative due to the consistent reduction of supporting structures and supporting work.
A tensioned 3D textile is to be attached to as few bracing and support points as possible and to reproduce the outer geometry. The lower layer is planned as a close-meshed textile with favourable fibres and forms the outer skin and shell level of the structure. The second textile layer above it, made of high-performance fibers with larger center-to-centre distances, creates the minimum reinforcement required for structural purposes. This is supplemented by force-flow-optimized reinforcing fiber strands and then overprinted with a minimum concrete cover, thus creating a shell. Due to the additional weight of the concrete, the textile serving as formwork experiences additional stress and deformation. This must be taken into account when building the support structure, but can also be used in the future to adjust the planned geometry.
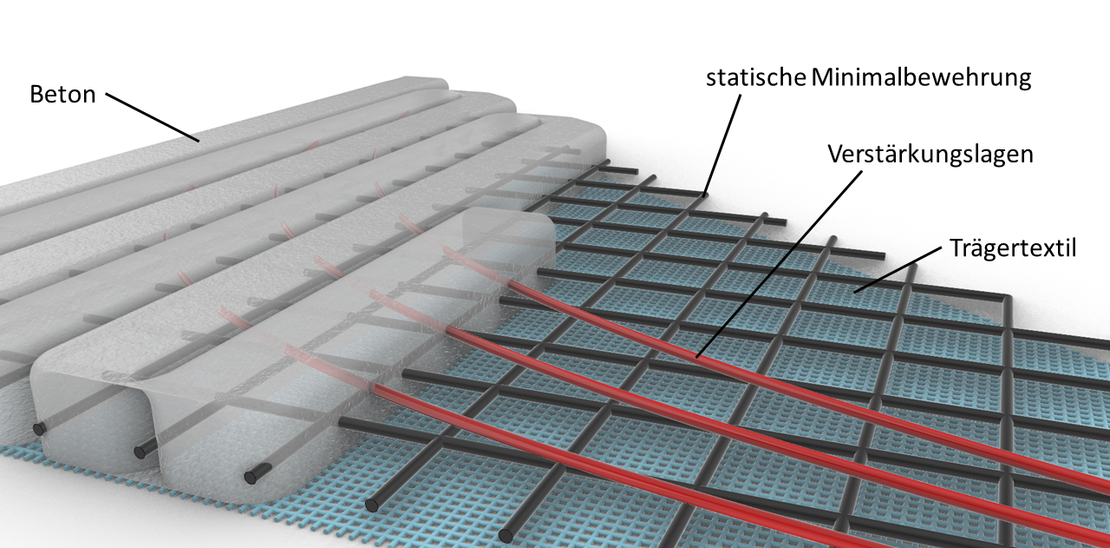
Team
![Prof. Dr.-Ing. Viktor Mechtcherine [Translate to English:] Viktor Mechtcherine](/fileadmin/_processed_/d/c/csm_Mechtcherine_Quadratisch_19756c182d.jpg)
D-01062 Dresden (Germany)
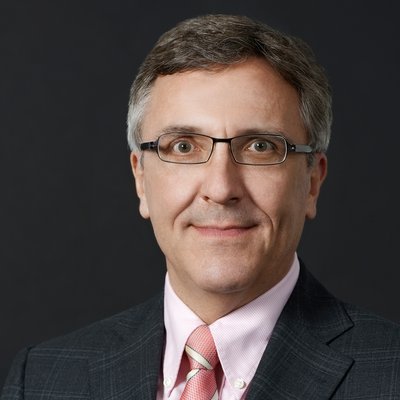
D-52074 Aachen (Germany)
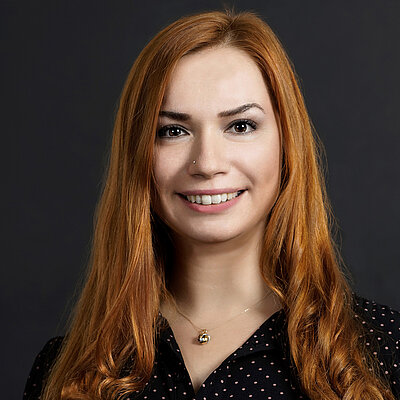
D- 52074 Aachen
![Dipl.-Ing. Tobias Neef [Translate to English:]](/fileadmin/_processed_/1/b/csm_Neef_Quadratisch_65c46070b2.jpg)
D-01062 Dresden (Germany)
Veröffentlichungen | Publications
Neef, T.; Dittel, G.; Scheurer, M.; Gries, T.; Mechtcherine, V. (2023) Utilizing Textiles as Integrated Formwork for Additive Manufacturing with Concrete in: Ilki, A.; Çavunt, D.; Çavunt, Y. S. [eds.] Building for the Future: Durable, Sustainable, Resilient – Proc. of fib Symposium 2023, 05.–07.06.2023 in Istanbul (Turkey), publ. in: Lecture Notes in Civil Engineering 349, Cham: Springer, p. 1285–1292 – DOI: 10.1007/978-3-031-32519-9_130
Scheurer, M., Neef, T., Dittel, G., Mechtcherine, V., Gries, T. (2023) Textile Reinforced Concrete Structures Additively Manufactured on Free-Standing Textile Formwork in: Harris, K. A.; Cardoso, D. C. T.; da Silva, F. A. [eds.]: Proc. of 11th Int. Conf. on Fiber-Reinforced Polymer (FRP) Composites in Civil Engineering (CICE 2023), 24.–26.07.2023 Rio de Janeiro (Brazil), 2023 – https://doi.org/10.5281/zenodo.8114263